Quand la technique de pointe s'unit au travail manuel
Chaque bas de compression passe entre de très nombreuses mains.
S'il est vrai qu'aujourd'hui, les bas de compression médicale sont fabriqués en grande partie sur des machines à tricoter de pointe, il faut encore beaucoup de travail manuel. Et cela ne s'applique pas seulement à la couture ou au remaillage, une technique d'assemblage de différentes pièces par une couture élastique et plate. À l'atelier de teinture, à la buanderie, au contrôle qualité ou encore à la préparation des commandes, les professionnels qualifiés ne sauraient être remplacés.
Venez jeter un coup d'œil dans les coulisses de notre production!
Le saviez-vous? Au cours du processus de fabrication, une paire de bas de compression passe par six départements de Juzo différents. Ce sont donc au moins douze personnes qui travaillent sur le bas et le contrôlent.
Deux procédés de tricotage en cohabitation
Tous les bas de compression ne sont pas identiques. En effet, il existe, pour les bas de compression, deux procédés de fabrication totalement différents pour lesquels on utilise des machines totalement différentes aussi.
Pour le procédé dit du tricot circulaire, on tricote – comme sur un tricotin – une sorte de tube rond sans couture, toujours en cercle.
Pour le tricot rectiligne, on confectionne en revanche une pièce textile à plat en tricot. Au cours d'une deuxième étape, cette pièce est cousue pour former un bas. Il est possible de tricoter très précisément en fonction des mensurations de chacun.
En raison de ces différentes techniques de fabrication, les bas de compression ont des propriétés différentes et sont destinés à différentes pathologies ou indications médicales.
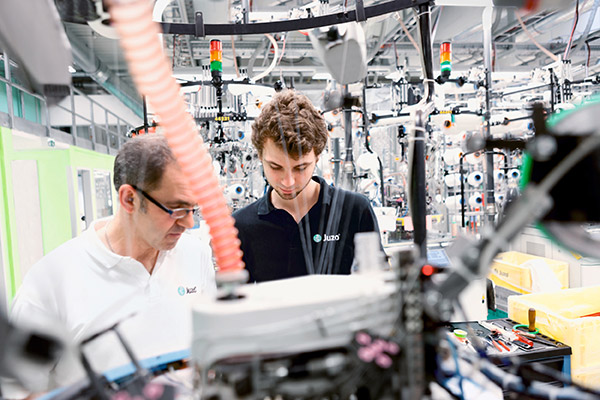
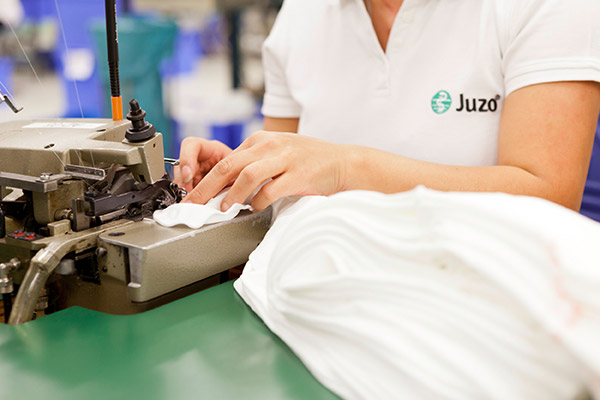
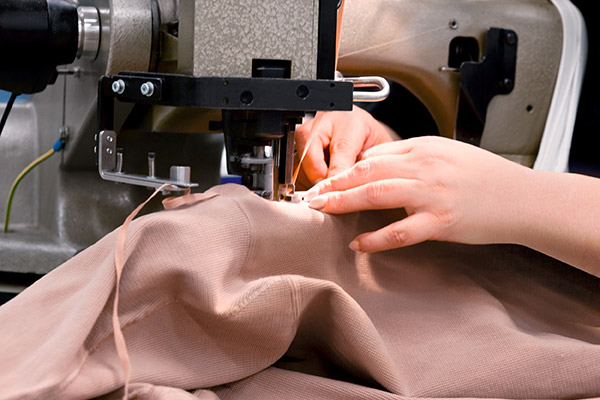
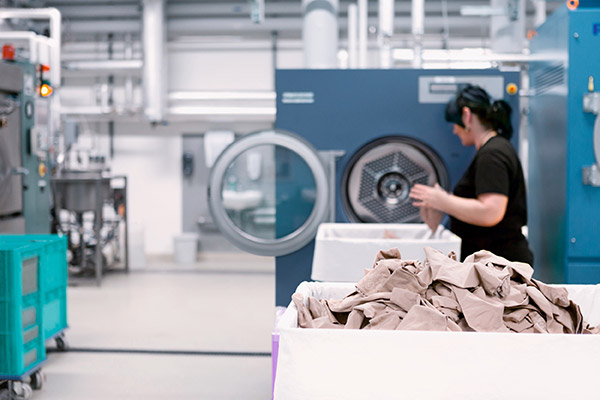
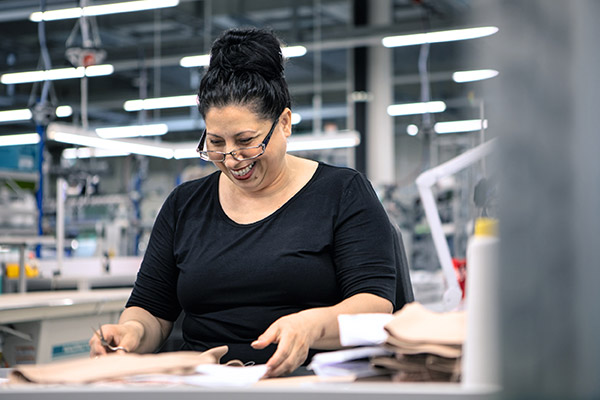
La qualité made in Aichach
Pour la fabrication des bas de compression, Juzo mise entièrement sur la qualité made in Aichach. Et il n'y a pas que la fabrication des bas. On trouve également sur place l'ensemble du processus de teinture ainsi que la mise en place des compléments comme les ourlets adhésifs, les parties abdominales et les pelotes. Ce sont donc tous les jours plusieurs milliers de pièces uniques sur mesure, spécifiques aux patients qui sont produites.