Hightech trifft Handarbeit
Jeder Kompressionsstrumpf geht durch zahlreiche Hände
Auch wenn medizinische Kompressionsstrümpfe heutzutage weitgehend maschinell an Hightech-Strickmaschinen gefertigt werden, so ist noch immer jede Menge Handarbeit erforderlich. Das gilt nicht nur in der Näherei oder beim Ketteln, einer Technik zum Verbinden von Einzelteilen mit einer elastischen, flachen Naht. Auch in der Färberei, Wäscherei, Qualitätskontrolle sowie beim Kommissionieren sind qualifizierte Fachkräfte nicht zu ersetzen.
Blicken Sie hinter die Kulissen unserer Produktion!
Wussten Sie schon, dass ein Paar Kompressionsstrümpfe im Laufe des Herstellungsprozesses sechs Abteilungen bei Juzo durchläuft? Dabei wird es von mindestens zwölf Personen bearbeitet und kontrolliert.
Zwei Strickverfahren unter einem Dach
Kompressionsstrumpf ist nicht gleich Kompressionsstrumpf. Denn für Kompressionstrümpfe gibt es zwei völlig unterschiedliche Herstellungsverfahren mit komplett unterschiedlichen Maschinen.
Beim sogenannten Rundstrickverfahren wird, wie bei der Strick-Liesel, immer im Kreis herum nahtlos eine Art runder Schlauch gestrickt.
Beim sogenannten Flachstrickverfahren wird hingegen ein ebenes Stoffstück als Gestrick angefertigt. Dieses wird dann in einem zweiten Schritt zu einem Strumpf zusammengenäht. Dabei kann sehr genau nach den jeweiligen Körpermaßen gestrickt werden.
Bedingt durch die unterschiedlichen Herstellungstechniken haben die Kompressionsstrümpfe unterschiedliche Eigenschaften und sind für unterschiedliche Erkrankungsbilder bzw. medizinische Indikationen vorgesehen.
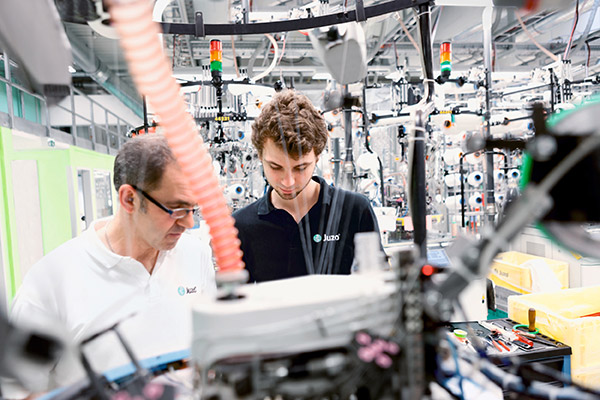
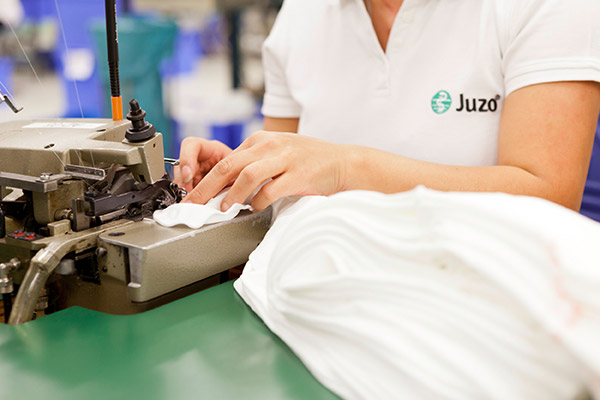
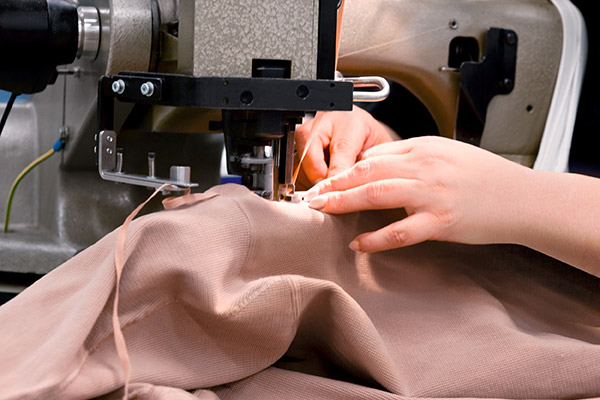
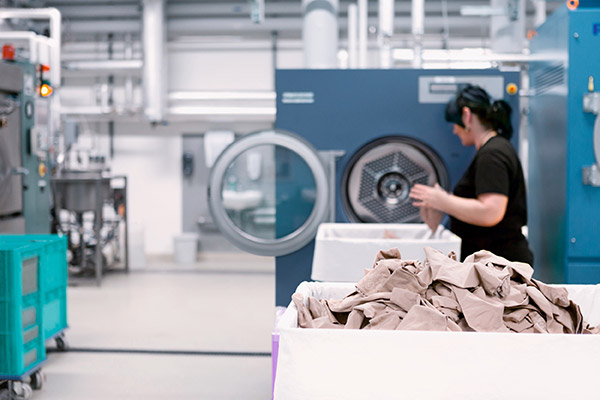
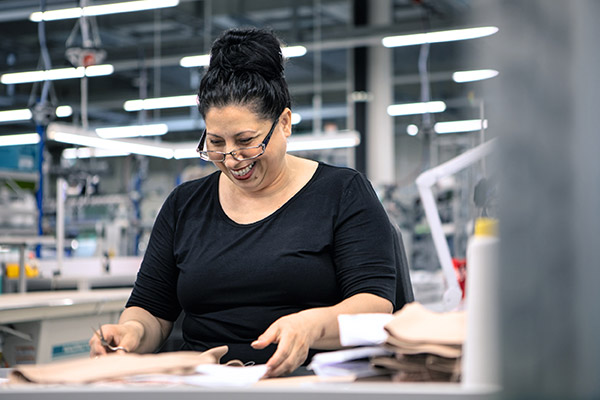
Qualität Made in Aichach
Bei der Herstellung von Kompressionsstrümpfen setzt Juzo komplett auf Qualität Made in Aichach. Neben der Herstellung der Strümpfe finden auch der gesamte Färbeprozess sowie die Ausstattung mit Extras wie Hafträndern, Leibteilen und Pelotten vor Ort statt. Dabei fließen täglich mehrere tausend patientenspezifische Einzelanfertigungen nach Maß mit in die Produktion ein.